Mantenimiento Total
Productivo (Total
Productive Maintenance)
Es el sistema japonés de
mantenimiento industrial a partir del concepto de “mantenimiento preventivo”,
este sistema de gestión que evita todo tipo de pérdidas durante la vida entera
del sistema de producción, maximizando su eficacia e involucrando a todos los
departamentos y personal.
El TPM es un poderoso
concepto que nos conduce cerca del ideal sin averías, defectos no problemas de
seguridad. Este amplia la base de conocimientos de los operarios y del personal
de mantenimiento y los une como un equipo cooperativo para optimizar las
actividades de operación y mantenimiento.
Busca mantener los equipos
en disposición para producir a su capacidad máxima productos de la calidad
esperada, sin paradas no programadas, es decir:
- -
Cero averías
- -
Cero tiempos muertos
- -
Cero defectos debido al mal mantenimiento de
los equipos

-
Sin perdidas de rendimiento o de capacidad productiva
debido a estos equipos
Es una estrategia compuesta
por una seria de actividades ordenadas que una vez implantadas ayudan a mejorar
la competitividad de una organización, ya que ayuda a crear capacidades
competitivas a través de la eliminación rigurosa y sistemática de las
deficiencias de los sistemas operativos.
Objetivos del TPM
1.
Ayuda construir capacidades competitivas
desde las operaciones de la empresa, flexibilidad y capacidad de respuesta,
reducción de costos operativos y conservación del conocimiento industrial.
2.
Que los equipos operen sin averías y fallas,
eliminar toda clase de perdidas, mejorar la fiabilidad de los equipos y emplear
la capacidad industrial instalada.
3.
Minimizar los inventarios e incrementar la
productividad.
4.
Fortalecer el trabajo en equipo, mejorar el
ambiente laboral y la seguridad.
Beneficios
Beneficios con respecto a la
organización
1.
Mejora de calidad del ambiente de trabajo
2.
Mejor control de las operaciones
3.
Incremento de la moral del empleado
4.
Creación de una cultura de responsabilidad,
disciplina y respeto por las normas
5.
Aprendizaje permanente
6.
Creación de un ambiente donde la
participación, colaboración y creatividad sea una realidad
7.
Redes de comunicación eficaces
Beneficios con respecto a la seguridad
1.
Mejora las condiciones ambientales
2.
Cultura de prevención de eventos negativos
para la salud
3.
Incremento de la capacidad de identificación
de problemas potenciales y de búsqueda de acciones correctivas
4.
Entendimiento del porqué de ciertas normas,
en lugar de como hacerlo
5.
Prevención y eliminación de causas
potenciales de accidentes
6.
Elimina radicalmente las fuentes de
contaminación
Beneficios con respecto a la
productividad
1.
Elimina perdidas que afectan la productividad de la plantas
2.
Mejora la fiabilidad y disponibilidad de los
equipos
3.
Reducción de los costos de mantenimiento
4.
Mejora de la calidad del producto final
5.
Menor costo financiero por recambios
6.
Mejora de la tecnología de la empresa
7.
Aumento de la capacidad de respuesta a los
movimientos del mercado
8.
Crea capacidades competitivas desde la
organización
Diferencias en el mantenimiento en tres niveles:
·
Operador: en tareas de mantenimiento como:
limpieza, ajuste, vigilancia de parámetros y reparación de pequeñas averías.
·
Técnico integrado. Una persona de
mantenimiento que trabaje de cerca con el equipo de producción, un repuesto
descentralizado: cada línea lo requiere, cada máquina.
·
Intervenciones de mayor nivel: revisiones
programadas, ajustes delicados.
Las 6 perdidas que efectúa una maquina parada
-
Pérdida de tiempo
-
Ajustes de maquina (pérdida de tiempo)
-
Marchas en vacío, esperas y detenciones.
-
Velocidad de operación reducida (el equipo no
funciona a su máxima capacidad)
-
Defectos en el proceso, producen perdidas
productivas
-
Pérdidas de tiempo propias de la puesta en
marcha de nuevo, al vacío, o periodo de prueba, etc.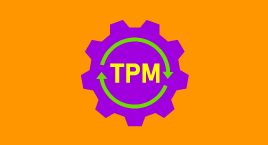
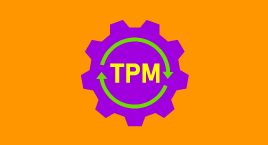
¿Cómo se implanta en la empresa?
Fase 1. Aseo inicial:
limpiar la máquina del polvo y brindarle un programa de lubricación.
Fase 2. Medidas para
descubrir las causas de la suciedad, el polvo y las fallas: se debe evitar las
causas de la suciedad, el polvo y funcionamiento irregular, mejora el acceso a
los lugares difíciles de limpiar, lubricar y reducir el tiempo que se necesita
para limpiar.
Fase 3. Preparación de
procedimientos de limpieza y lubricación: procedimientos estándar con el objeto
que las actividades de limpieza, lubricación y ajustes menores de los
componentes se puedan realizar en tiempos cortos.
Fase 4. Inspecciones generales:
checar e inspeccionar el equipo en busca de fallos menores y en la fase de gestación,
así como su solución.
Fase 5. Inspecciones autónomas:
listas de chequeo, implantación del mantenimiento preventivo periódico realizado
por el personal que opera la máquina.
Fase 6. Orden y armonía en
la distribución: crear estándares y procedimientos para la limpieza, lubricación,
inspección, mantenimiento de registros, gestión de la herramienta y del
repuesto.
Fase 7. Optimización y autonomía
en la actividad: desarrollar una cultura hacia la mejora continua en toda la
empresa.
Aspectos importantes:
1.
Para completar el programa varia de 2-3 años
2.
Utiliza el ciclo PHVA para su implantación
3.
Todos se deben involucrar
4.
Capacitación continua
Mantenimiento Total
Productivo (Total Productive Maintenance)
Comentarios
Publicar un comentario